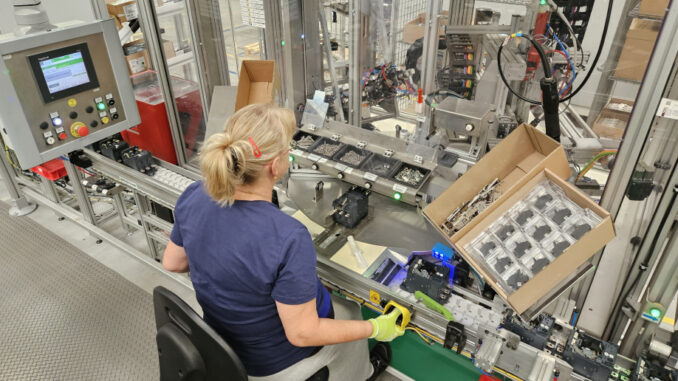
Sprawna logistyka w międzynarodowej korporacji jest decydująca dla osiągnięcia dobrych wyników. Wpływa także znacząco na proces produkcji. Po połączeniu tych dwóch procesów oraz przy uwzględnieniu ich śladu węglowego widać, ile jest jeszcze do zrobienia.
- Schneider Electric, będąc znaczącym międzynarodowym graczem w sektorze energetycznym, widzi, jak istotne na rynku stało się obniżanie śladu węglowego kupowanych komponentów i sprzedawanych później gotowych produktów.
- Nearshoring (zlecanie pracy firmie, która znajduje się najbliżej kraju) to sposób, by obniżyć koszty produkcji. Tańsza produkcja w Azji nie jest już najważniejsza.
- W fabryce w Bukownie zaczęto mieszać plastik z biomasą. – Chcemy, by nasz produkt był zielonym produktem – mówi WNP.PL Marcin Bednarz, dyrektor Schneider Electric.
- O logistyce w nowoczesnej fabryce będziemy rozmawiali już 3-4 października br. podczas konferencji Nowy Przemysł 4.0. Natomiast temat śladu węglowego firm produkcyjnych podejmiemy 5-6 października podczas PRECOP 28. Wydarzenia odbędą się w Międzynarodowym Centrum Kongresowym w Katowicach.
Pandemia, której skutkiem były zerwane łańcuchy dostaw, dotknęła każdą firmę w Europie. To efekt globalizacji i korzystania z możliwości kupowania oraz produkowania tam, gdzie bardziej się to opłaca.
Czas po covidzie to jednak moment na rewizję dotychczasowych polityk – liczy się minimalizowanie ryzyka i zapewnienie ciągłości produkcji.
– Jest to zawsze kompromis pomiędzy ceną a dostępnością produktu. Część komponentów wytwarzana jest w Azji, bo tak jest taniej. Trzeba jednak pamiętać, że i tam koszty produkcji stale rosną. Dlatego staramy się lokalizować nasze źródła w Europie Środkowo-Wschodniej. Naszą strategią jest to, by produkować tam, gdzie sprzedajemy. To wpływa też na dobór poddostawców – mówi WNP.PL Marcin Bednarz, dyrektor zakładu Schneider Electric w Bukownie.
Jak przyznaje szef tej małopolskiego fabryki – pod wieloma względami nadal opłaca się produkować elektronikę w Azji. Inaczej jest, gdy w grę wchodzi waga i wielkość produktu.
– Bierzemy pod uwagę nie tylko koszt wytwarzania, ale także i transportu. Szukamy dostawców, którzy są zlokalizowani blisko naszej fabryki. Koszt wytwarzania u nich może jest i wyższy, ale biorąc pod uwagę koszt transportu i brak konieczności magazynowania, może się to opłacać w stosunku do oferty np. z Chin – dodaje Bednarz.
Produkty z Polski na szarym końcu. Czarne jak nigdy wcześniej
Dodatkowym wyzwaniem przy planowaniu produkcji jest uwzględnianie śladu węglowego transportu, ale i kupowanych na rynku podzespołów oraz produkowanych u siebie gotowych produktów.
To, w wielu przypadkach, powoduje, że sprowadzanie części z Azji przestaje się opłacać.
Gorzej, że z podobnych przyczyn na konkurencyjności tracą także fabryki w Polsce.
– W naszej części Europy energia elektryczna w większości produkowana jest z węgla. Produkcja plastiku, z którego w dużej mierze zbudowane są nasze produkty, jest procesem energochłonnym. Czasem okazuje się, że dostawca z Europy Zachodniej – z Hiszpanii czy Francji – ma niższy ślad węglowy i to pomimo całego procesu transportu do Polski. To oczywiście efekt tego, że energetyka tych państw bazuje na OZE. Zatem lokalny dostawca nie zawsze jest najlepszym wyborem, bo jak najniższy ślad węglowy jest istotnym czynnikiem wpływającym na naszą decyzję – wyjaśnia dyrektor fabryki Schneidera w Bukownie.
Z ciekawostek: w fabryce tej, która zlokalizowana jest nieopodal Olkusza, do powszechnie wykorzystywanego tam plastiku dodawana jest biomasa.
– Ona wiąże się z plastikiem. Dzięki temu zużywamy mniej zasobów naturalnych, a to jest istotne dla coraz większej liczby naszych klientów – tłumaczy Bednarz.
Logistyka na kontynencie. Niby daleko, ale jednak sprawniej
Schneider, którego fabryki zlokalizowane są na trzech kontynentach, stara się optymalizować koszty transportu. Kluczowe dla dystrybucji jego produktów są centra dystrybucyjne. W Europie jest ich kilka.
– Najbliżej nas jest zlokalizowane w węgierskim Budapeszcie, skąd zaopatrywani są klienci m.in. z Polski. Klienci, realizując inwestycje, kupują nie tylko nasz produkt, ale wiele komponentów, które umożliwiają wyposażenie potrzebnego im systemu. Bukowno dostarcza wyłączniki. W fabrykach Schneider Electric ulokowanych w innych częściach Europy produkowane są pozostałe części oferty. Klient kompletuje zamówienie, którego składowe pochodzą z różnych miejsc. Wszystko trafia więc do centrum dystrybucyjnego, w którym można skompletować całość – tłumaczy szef zakładu w Bukownie.
Jak zauważa nasz rozmówca, sporo – po pandemii – zmieniło się także jeśli chodzi o sposób produkcji w zakładach Schneidera. Skończył się czas, gdy magazynowano surowce, półprodukty czy podzespoły „na zapas” w obawie przed niestabilnością łańcuchów dostaw.
– Wróciliśmy już do normalności. Naszą ambicją jest: better than normal. Jesteśmy topową firmą na świecie, jeśli chodzi o łańcuch dostaw dla naszych klientów. Potwierdza to ranking Gartnera, w którym w 2023 roku po raz pierwszy uplasowaliśmy się na pierwszym miejscu wśród najlepszych 25 firm w obszarze Supply Chain. Wynika to z cyfrowych rozwiązań, które implementujemy w systemie zarządzania naszymi przepływami – komentuje Marcin Bednarz.
Cyfryzacja i robotyzacja. Człowiek ramię w ramię z cobotem
Schneider w Polsce wykorzystuje zaawansowane systemy ERP do zarządzania procesem zakupowym i dostosowaniem do niego tempa produkcji w fabrykach.
10 lat temu w Bukownie rozpoczęto także robotyzację produkcji. Zaczęło się od zakupu jednej maszyny.
– Wdrożenie pierwszego robota nie dość, że odciążyło pracownika, to zwiększyło jego produktywność oraz dokładność wykonywanych czynności. Po tym pierwszym doświadczeniu zdecydowaliśmy się zbudować całe linie z wykorzystaniem robotów – mówi Rafał Ziętak, dyrektor działu technicznego Schneider Electric w Bukownie.
Zaczęli od prostych robotów Scara, które przenosiły obiekty. Kolejne lata to już inwestycje w roboty współpracujące z człowiekiem. Wykorzystywany jest także cobot, który pracuje już nie w zamkniętej klatce, a ramię w ramię z operatorem.
Roboty spowodowały ograniczenie liczby pracowników. Po modernizacji linii produkcyjnej pracownicy zostali zaangażowani na inne sektory produkcji. Niezbędni są ludzie, którzy potrafią je zaprogramować, utrzymywać w odpowiednim stanie.
– Naszą intencją nie było nigdy zwalnianie pracowników ze względu na implementację robota. Wręcz przeciwnie – oni byli zawsze przesuwani na inne stanowiska, by utrzymać ich zatrudnienie – zapewnia dyrektor działu technicznego w Bukownie.
Zatrudnienie w zakładzie w Bukownie nie spada głównie dzięki decyzji centrali koncernu o zwiększaniu tam produkcji.
– Zainwestowaliśmy w pierwszego robota, który odbiera gotowe produkty. To jest platforma typu AGV, która jeździ autonomicznie po hali. W grudniu tego roku będziemy wprowadzać kolejnego takiego robota – uzupełnia Rafał Ziętak.
Jak dowiadujemy się w Schneiderze – koszty wdrożenia robotów AGV są znaczące, ale „nadal akceptowalne”.
Źródło: wnp.pl